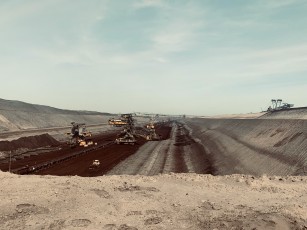
- read
- Daniele Paganelli
Before showing their stunning graphics in your interior lights or in the sun as a floor, before even entering the furnace, material scientists thoroughly look at ceramics in the light of X-Rays. Two analytical techniques, X-Ray Diffraction (XRD) and X-Ray Fluorescence (XRF) are routinely performed on raw materials to determine, respectively, their mineralogical and chemical composition. In both cases the material is irradiated by X-Rays, but different effects are then measured by the respective instruments.
Fluorescence is based on the excitation underwent by atoms when an X-Ray hits them: the decay from excited state emits a photons with characteristic wavelengths and intensities uniquely dependent on the element and its concentration in the sample.
The typical result of an XRF analysis is the composition expressed as element oxide concentration percentages. XRF is fast, reliable and precise, although not all elements can be identified with this technique.
Diffraction, in contrast, measures the intensities and scattering angles of the X-rays passing through or being reflected by the sample are measured and correlated with the most probable structures of the crystal lattices and their abundance.
The result of an XRD analysis is the mineralogical composition expressed as percentages of mineral structures concentration. XRD is intrinsically probabilistic: the spectra must be fitted against thousand of patterns produced by known mineral structures. The mathematically best solution not always makes sense: the operator must know which pool of minerals are reasonable to be found in that particular material and manually exclude extravagant species.
Apparently, chemical and mineralogical composition are two incommensurate material properties, like the weight and the color. While this is certainly correct in general, in the specific case of materials largely comprised of identifiable mineral structures we must expect a strong correlation between the two results. Minerals obviously have their chemical composition: by decomposing the mineralogical formula of a raw material into its base oxides, we obtain a chemical composition which should match closely the one measured with the fluorescence. But this is usually not the case, mostly because of the uncertainties associated with the diffraction pattern-matching, and partly because of the amorphous phases eluding analysis. Having access to both XRD and XRF data, it is good practice to harmonize the two with Ceramics Genome.
Reformulation of a mineralogical composition
The Ceramics Genome glossary, a Formulation document encapsulates the information required to describe the process of finding the mixture of materials satisfying multiple constraints while minimizing a cost function. The input variables are:
- A pool of materials that the minimizer can mix in order to obtain the target outcome. The cost of each material can either be defined in the material document, or locally in the pool definition. Each material in the pool also has its own maximum/minimum ranges.
- The target oxides composition, a table of oxides quantities as percentages, with optional individual min/max ranges. While minimizing the cost function, the minimizer will search for a mixture of materials in the pool that, decomposed, would give an oxides composition near to that target.
- An allowed tolerance between the target oxides composition and the solution.
- A Weight Loss constraint that the final mix must respect.
- The cost function – green or fired cost or any numerical property.
Upon execution, the Formulation document returns a composition of materials selected from the pool which is within tolerance from the target oxides table. The Formulation document is perfectly apt to the task of harmonizing XRD guesses with XRF measurement.
-
The target oxides composition is compiled with the results of the XRF analysis. It will rarely close at 100%, but in order for the minimizer to succeed the input must (and will) close to 100%. What remains (usually less than 1%) will be automatically added under the special Unknown Residual material.
-
Most of the missing material will be volatile (water, carbonates decomposition, C/S combustion): the Weight Loss must be expressed as a custom constraint, with a minimum and maximum value extremely near (or identical) to the measured LOI.
-
The pool of materials available to the minimizer lists all the most probable minerals returned by the XRD and according to operator’s experience. Optionally, ranges around the XRD results can be expressed for each mineral (with ranges around the measured value of, for example, +- 5%). The Unknown Residual special material will be automatically added upon execution.
-
The tolerance can be set large, even 10%, as the cost function will be “Target Distance”. This means the cost will simply be equal for all materials, regardless of their memorized cost, so the optimizer will just try to reach the solution nearest to the target oxides. The distance will be calculated on the fired quantities.
-
The minimize tolerance flag must be activated.
The result of this Formulation document will be a mineralogical composition having the nearest chemical composition to the XRF measurement and within the defined boundaries from the XRD estimation.